Renowned for its quality and durability, wool is the most recycled apparel fibre in the world, offering an unparalleled circular solution. The Woolmark Recycled Wool product specification offers supply chain and consumers added confidence in quality as products undergo and pass the same tests as virgin wool fabrics to guarantee the same features.
With a rich 200-year recycling heritage, wool provides an opportunity to improve the linear fashion and textile industry's current practices. Research by the Centre for Colour and Textile Science at Leeds University has shown that wool products have the potential for two or more uses or ‘lives’ and a total ‘active life’ of 20-30 years, supporting the transition to circular business models and design.
Why Recycled Wool?
Up to 6% of all wool fibre undergoes mechanical recycling. Recycled wool offers extensive benefits: from reducing environmental impact and conserving resources to ensuring durability and versatility in every garment.
Woolmark-Certified Recycled Products
The Woolmark Certification Program’s recycled wool certification scheme focuses on products made from pre-consumer and post-consumer wool products that have been reclaimed and reprocessed into new yarn, knitted or woven fabric, apparel or footwear. Recycled Wool is a sub-branding to the Woolmark logo suite, indicating that a product is made of either 100% recycled wool or a wool blend that contains at least 20% recycled wool with a fibre diameter ≤22.5um.
A certificate substantiating the recycled wool content of a product is required to use the logo on finished products. The Global Recycled Standard (GRS) and Recycled Claim Standard (RCS) set the criteria to verify and track the recycled content of materials and are deemed acceptable.
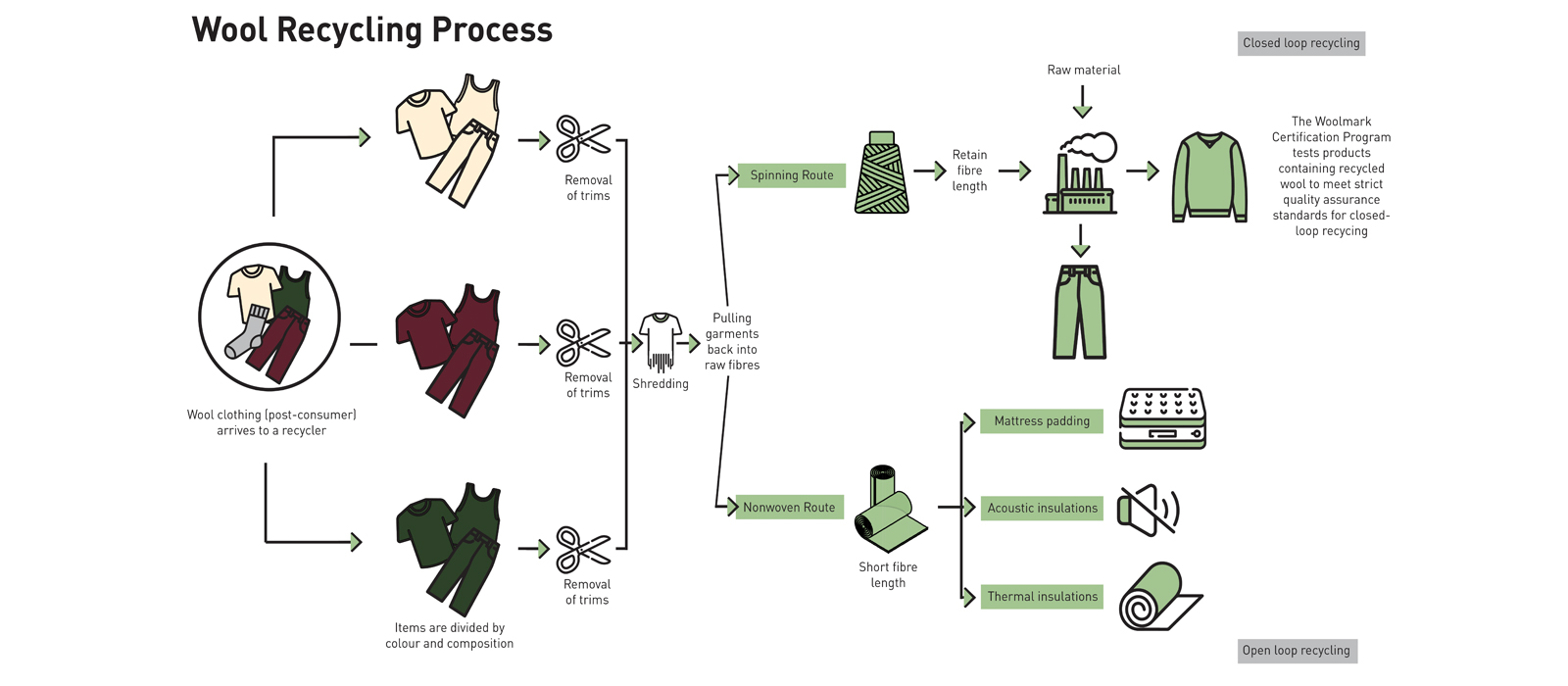
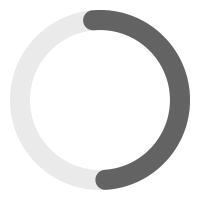
The closed-loop mechanical process involves collecting and sorting wool garments or textiles based on colour and condition, which then undergo a series of mechanical processes to break them down into raw wool fibres to create yarn for new products.
Sorting: Each wool product is sorted based on factors covering fibre type, colour and quality.
Cleaning: Trims such as labels, buttons and zippers are removed from the product.
Shredding or Cutting: Wool materials are shredded or cut into smaller pieces.
Carding: Cleaned wool fibres are carded to align the fibres in a parallel arrangement of uniform length and thickness to prepare them for spinning.
Spinning: Carded wool fibres are spun into yarn using spinning machines. The wool fibres are twisted together to create a continuous strand of yarn.
Weaving or Knitting: The yarn produced can be woven or knitted into fabric, depending on the desired result.
Manufacturing: The woven or knitted fabric is used to make new wool products including clothing, blankets upholstery and more, which can be reintroduced into the market. This completes the closed-loop recycling process.
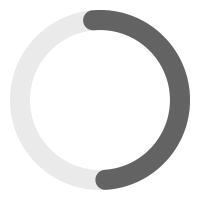
The open-loop system is essentially ‘down cycling’ where wool products are pulled apart, often blending with other materials, and reprocessing into alternative products such as insulation or mattress padding.
Collection: Wool products including clothing, carpets, upholstery, and textile waste are collected.
Sorting: Each wool product is sorted based on factors covering fibre type, colour and quality.
Cleaning: Trims such as labels, buttons and zippers are removed from the product.
Processing: The cleaned wool undergoes various processing methods, depending on the desired product. Processing can involve mechanical processes, chemical or thermal treatments.
Get Certified
Suppliers at any stage of the supply chain – spinners, knitters or weavers – can certify their recycled wool products and pass on their certification to brands to use the Recycled Wool logo.